Aircraft design process Wikipedia
Table Of Content
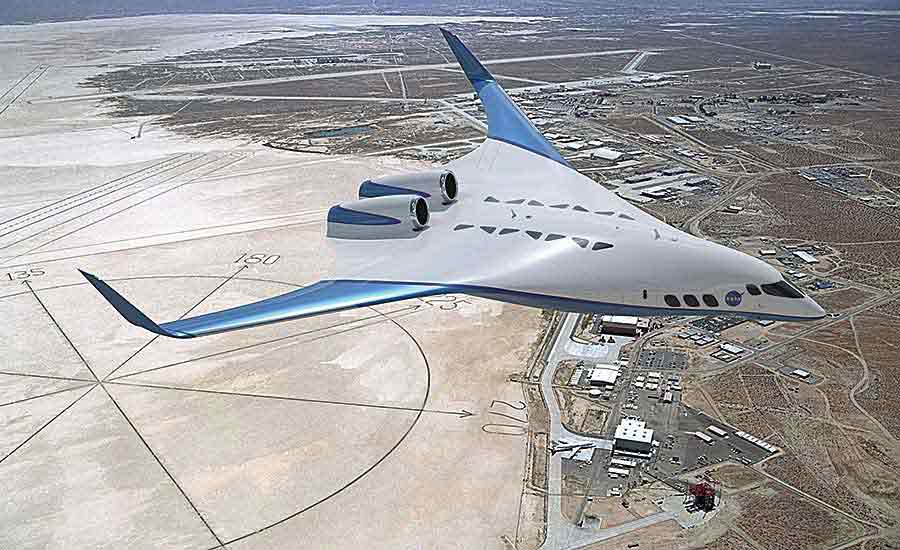
Junior engineers were hired at inflated salaries and higher cost to the taxpayer, but a lack of domain expertise contributed to significant cost and schedule delays for the ill-fated Comanche program. It takes years to build up a talented aircraft design team, but only a moment to lay them off. In the case of national defense, citizenship and security clearance requirements make hiring and training specialized rotorcraft engineers all the more difficult, expensive and time consuming. Start developing a network of industry contracts “early in your engineering education,” advises Wolz. “Look for opportunities to network, and for practical work experience through internships and co-ops (cooperative education programs).” Sturdza notes he began working with Aerion when writing his Ph.D. thesis on laminar flow technology, inspired by Aerion’s founder. “Sending out your resume is not nearly as effective as having some sort of relationship” with a potential employer, Sturdza says.
Astronauta de la NASA Marcos Berríos
You have to recognize that you have to work at it and grow, and earn respect and opportunities,” Wolz says. This stage includes back of the envelope calculation, where all the ideas are brainstorm. As the design continues to be revised it will undergoe many transformations to conform to the fit/form/functions that are desired by the end user or purchaser. These basic functions are brought together to create the initial configuration design which is used to discuss different possibilities with the consumer during a conceptual design review.
Defining cabins for
Aircraft architects establish the overall concept and integrate the solutions to ensure a balanced design meeting all requirements, while aerodynamicists find the optimum wing shape and provide aerodynamic data for performance, loads and handling qualities. This article deals with powered aircraft such as airplanes and helicopter designs. The card is available exclusively for new and existing Delta SkyMiles Reserve and Reserve Business Card Members from April 25 through June 5, 2024, while supplies last.
Humans in Space
An aircraft’s development brings together multidisciplinary teams that work in a highly collaborative environment, uniting teams of different skills including various engineering disciplines, along with manufacturing, customer services and procurement. Bell and Sikorsky were downselected in March 2020 and each hired hundreds of engineers to support the development of these next-generation rotorcraft, meeting the Army’s challenging timeline. A major change for CCA, compared to past GA-ASI programs like MQ-1s and MQ-9s, was the expectation from the beginning that many will be built.
Designing aircraft to reduce environmental impact
The new design comes after recent enhancements made to the Delta SkyMiles American Express Cards to improve the travel experience and deliver everyday value to Members, both in the air and on the ground. That drove a design that should be easily scalable, so much so that GA-ASI expects it could beat the Air Force’s target schedule by 50%. In the announcement, the Air Force said it expects the first increment to be operational by 2028, with a potential down select in 2026. Alexander also says the company’s design should be better than the Air Force’s requirements. General Atomics President David Alexander told Aerospace DAILY that the company’s plan from the beginning was to design a platform that could be built quickly and at a large scale.
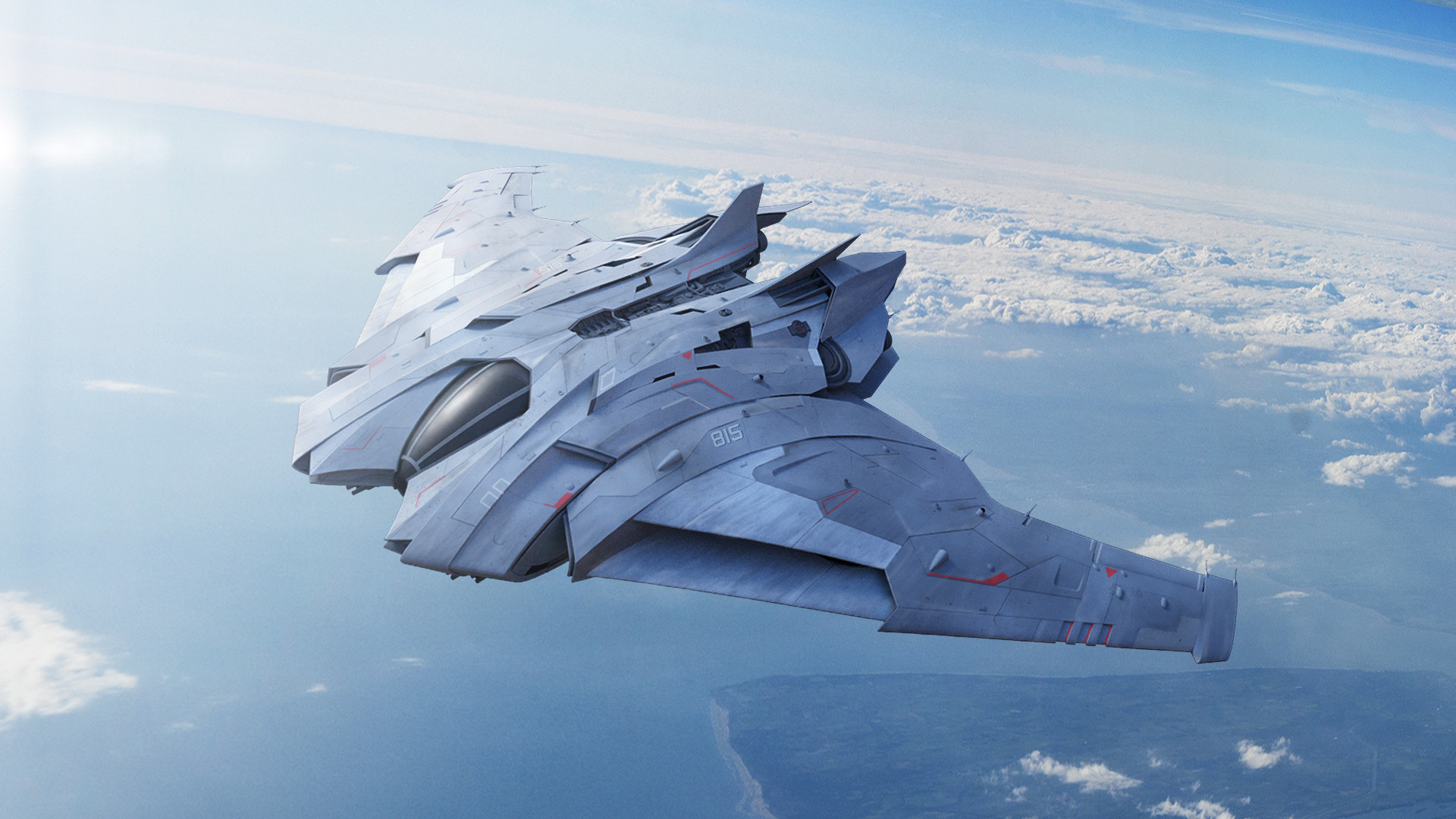
This phase simply deals with the fabrication aspect of the aircraft to be manufactured. Other than the Bell FLRAA program, none of the US military services has an active development program underway for a new rotorcraft. When these programs advance to the contracting phase, the US rotorcraft industry will be able to staff up again as necessary.
One of Europe’s Biggest Air Shows Featured Every Kind of Aircraft, From Drones to Business Jets
AIAA Announces 2024 Design/Build/Fly (DBF) Competition Winners - PR Newswire
AIAA Announces 2024 Design/Build/Fly (DBF) Competition Winners.
Posted: Mon, 22 Apr 2024 12:40:00 GMT [source]
Air Force Secretary Frank Kendall has given industry a planning figure of about 1,000 for the aircraft. Computational fluid dynamics (CFD) combines applied mathematics, physics and high-performance computing. It’s used to understand how air moves over complex shapes, helping designers maximise lift and minimise drag to make an aircraft as efficient as possible at both low and high speeds. Another way to get more fuel efficiency out of an engine is to change its configuration in terms of how air flows through it and at what pressures and temperatures.
You'll also be able to set the rpm's or throttle setting (if you specified a motor for all your propellers) of the propellers. Now, with the propeller selected, you can modify elements of it's geometry, including the number of blades, the pitch , diameter, and airfoil characteristics. You can even specify the characteristics of your power system including the motor, esc, and battery. MachUp will then use this information to give you an estimate of how the propeller will operate at a given flight condition and throttle setting. “A difference in generations” is appearing in the aeronautical workforce, Wolz says, with today’s hires eager “to get on the fast track.” But careers typically progress less rapidly than the aircraft the field creates.
Blyth also recommends considering the type of company you want to work for — “a small company where you’re involved in every aspect of design and development, or a larger company where somebody might specialize in brakes” — before plunging ahead. One of the designs that came out of earlier research projects into future aircraft designs, the TTBW is essentially a classic tube and wing airplane but with a wing that is extremely long and thin. So long and thin, in fact, that it needs a little help on both sides of the fuselage to hold it up. In the feasibility and concept phases, market expectations and requirements are explored. Different options are combined to come up with an overall aircraft concept with the latest technologies, structural concepts and systems architectures. The result is a product specification to start detailed design of parts and the specification of system elements from equipment suppliers.
For example, a company might have identified that there is a growing demand for small private jets. In the inital problem definition stages it is crutial to first identify the key requirements of the new product then to determine how realistic it is to create this product through a feasibility analysis. Although other revolutionary aircraft designs have been studied – such as the Double Bubble and Blended Wing Body – the TTBW technology shows the most promise for being ready the soonest. But if I can use electricity to help me out with certain parts of the flight envelope, I can design my engine differently and make it more efficient overall,” Kenyon said.
The Flight Design CTLSi is the newest version of the popular CT series optimized for the Light Sport Aircraft rules of the United States. Flight Design USA has delivering 56 of the CTLSi with the Rotax 912is since 2012 and the model is the most popular offered. Offered only in “fully loaded” configuration as the CTLSi GT 2020, the CTLSi contains everything a modern aircraft should. “Defense customers [need them] quite quickly, then they stay in service for a long time,” says Steve Patrick, vice president of Bombardier Defense. “A phrase we use quite a lot is ‘capability at the speed of relevance.’” Echoing Brana, Patrick says that “commonalities of supply chain and engineering processes” avoid the need for constant reinvention. In this tab you get to set various aspects of the flight condition including the velocity, angle of attack, and any control surface deflections.
Cadets design planes to solve problems • United States Air Force Academy - Air Force Academy
Cadets design planes to solve problems • United States Air Force Academy.
Posted: Thu, 07 Dec 2023 18:49:09 GMT [source]
Following these is a preliminary design review, to ensure the concept can become a reality and for a reasonable price. So, a company or an individual wants to begin the aircraft design process… Have you ever wondered where to start? Thankfully, there are a few key principles which can help guide engineers through any design process, through improved analysis the fundamentals of design, this same process can be refined into a aircraft design process. However, before moving on to design process, it is important that an engineering product follows a very similar design approach.
This menu contains all of the different analyses that MachUp can do on your aircraft. To run an analysis, simply select the analysis you want and click 'Update Results'. Note that depending on the analysis you want to run, it may take anywhere from 1-30 seconds, so you may have to learn a bit of patience. If you get frustrated, just think about how much faster this is than doing all of these extremely complex calculations using a slide rule. It’s a beautiful thing, a kind of computerised wind tunnel,” grins Airbus’ Head of Aerodynamics Simon Galpin.
Aircraft conceptual design involves sketching a variety of possible configurations that meet the required design specifications. Fundamental aspects such as fuselage shape, wing configuration and location, engine size and type are all determined at this stage. Constraints to design like those mentioned above are all taken into account at this stage as well.
The company’s S-92 is being delivered to the Marine One Presidential Helicopter Squadron and to civil and military customers around the world, albeit in small numbers. The transfer of aeronautical tech also continues to advance the business-jet world. Take the fly-by-wire hardware that first appeared on General Dynamics’ F-16 fighter. These digital flight control systems (DFCS) allowed for faster and more agile fighter jets and provided more flight consistency than conventional controls. The technology later appeared on the Dassault Mirage 2000, became a primary feature on the Falcon 7X, and is now standard across the Falcon line.
Comments
Post a Comment